Plasma & Wire
Our patented RPD® process is based on plasma arc; titanium wire is precisely melted in a controlled manner in an inert argon gas environment.
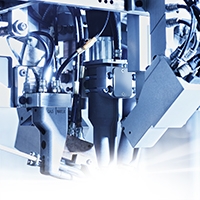
Rapid plasma deposition℠ is the platform technology that brings manufacturing into the twenty-first century.
Pounding and forging metal into unique shapes is almost as old as humankind itself. Norsk Titanium reimagines traditional forge-based manufacturing by creating advanced metal objects through revolutionary additive manufacturing technology. Norsk Titanium provides treatment of materials, namely metals and metal ores by plasma arc additive layer manufacturing. The result is greater strength and durability delivered in an on-demand environment with an improved environmental footprint.
In our patented rapid plasma deposition® (RPD® ) process, titanium wire is precisely melted in an inert, argon gas environment. The process is monitored more than 600 times per second for quality assurance.
Rapid plasma deposition® technology is the ultimate in additive manufacturing. Titanium wire is melted in an inert atmosphere of argon gas and precisely and rapidly built up in layers to a near-net-shape part. The result is significantly less machining, and ultimately, a 50%–75% improvement in buy-to-fly ratio compared with conventional manufacturing methods.*
Reduced machining also leads to less tooling and energy usage, which are significant cost drivers for titanium parts. The end result is reduced production cost for finish titanium parts, ultimately benefiting the customer.
* Weight of raw material and weight of finished part
Norsk Titanium has focused on metallurgy from day one. Our organization was founded by scientists and engineers who believed: If we manage to get to the highest levels of material quality, everything else can be solved.
The superior metallurgy is delivered consistently, across part geometries, RPD® machines, and Norsk Titanium sites in the United States and Europe. Our high quality material is ultimately creating a real alternative for our customers to swap to commercial production of additive manufactured parts.
Superior metallurgy implies:
* Reference to standards for forged titanium
Norsk Titanium has become synonymous with both disruptive innovation and 100% reliability in delivering our FAA-approved products.
Norsk Titanium’s RPD® technology is a platform technology that transcends borders, alloys, and sectors. RPD® will bring resource and production efficiencies to new levels.
RPD® is an adaptable machine applications technology. It is easily customized for specific applications to achieve entitlement levels of productivity.
MERKE IV: THE MACHINE BEHIND RAPID PLASMA DEPOSITION®
Our patented RPD® process is based on plasma arc; titanium wire is precisely melted in a controlled manner in an inert argon gas environment.
Via a lean, optimized production environment, we can enable production of safety-critical finished titanium parts from wire to finished component in 150 feet (50 meters).
Our patented RPD® process is based on plasma arc; titanium wire is precisely melted in a controlled manner in an inert argon gas environment.
Via a lean, optimized production environment, we can enable production of safety-critical finished titanium parts from wire to finished component in 150 feet (50 meters).
Each MERKE IV® machine can produce 10–20 metric tons annually, depending on part size and geometry.
The RPD® parts are so-called near-net-shape, which means that they are close to the net shape in terms of weight and configuration compared with traditional forgings. The RPD® parts are completed to net-shape by finish machining centers.
The MERKE IV® is our 4th generation production machine. Using our patented RPD® process, the MERKE IV® transforms titanium wire into complex components suitable for structural and safety-critical applications. Depending on part size and geometry, each MERKE IV® machine can produce 10–20 metric tons annually. MERKE IV® Norsk Titanium RPD® technology takes on-demand metal additive manufacturing to the stars and beyond by transforming the way aerospace companies produce structural components.
Specifications:
Titanium wire is currently utilized in Norsk Titanium’s RPD® technology due to requirements in the heavily regulated aerospace industry. Nickel alloys, tool steel, and stainless steel are all applicable to the RPD® platform.
Norsk Titanium is a Tier 1 Supplier to Commercial Airframe and Engine OEMs and is committed to cost-reducing aerostructures and jet engines for the world’s premier aerospace manufacturers. RPD® is the world’s first FAA-approved, 3D-printed, structural titanium, delivering substantial lead-time and cost savings for aerospace, defense, and commercial customers. By delivering customers unprecedented application opportunities, Norsk Titanium will accelerate revolutionary changes to the world’s metal manufacturing processes.
RPD® is the platform technology that brings manufacturing into the twenty-first century. Literally thousands of parts can be created at lower cost, better lead time, and at near-net shape. RPD® transforms the way aerospace-grade structures are produced. By melting titanium wire in an inert argon atmosphere, near-net shape parts are precisely and rapidly built up and require little additional machining. The customer receives the parts at a lower price compared to traditional forging techniques, with additional advantages such as less waste, machining, tooling, and energy usage.
The flexibility of the Norsk Titanium RPD® process allows us to print the forging form that can then go into the forging die. This reduces material, lead-time, and the capital of several of the forging dies.
The patented RPD® process is capable of printing on any suitable substrate. This means that complicated features of forgings can be added after the material is forged. Thus, a more simplified forging can be used to make a more complicated part. It also means that features such as bosses on turbine engine cases can be added to ring-rolled forgings. Forge-then-print reduces the amount of material in the ring-rolled forging as well as the machining required.