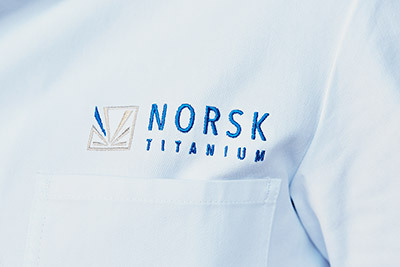
Norsk Titanium Produces Space Demonstration Hardware
Supports European Space Agency Technology Research Programme
Farnborough, UK – July 16, 2018 – Norsk Titanium (Norsk), the world’s first FAA-approved supplier of aerospace-grade, additive manufactured, structural titanium components, has produced an Expansion Nozzle demonstrator in support of the European Space Agency’s Technology Research Programme (TRP).
The TRP is an European Space Agency (ESA) technology development effort supporting all of ESA’s fields of activity across the entire spectrum of technical disciplines, providing the technological nucleus for most future developments. Norsk was awarded a TRP contract with the ESA in 2014 to explore the application of Norsk’s Rapid Plasma Deposition™ (RPD™) process to space applications.
Through the TRP contract, Norsk has refined its material characterization and quality assurance processes, while providing ESA valuable insight into the application of additive processes to their unique needs.
The culmination of this effort was the production of an Expansion Nozzle demonstrator. The expansion nozzle utilizes the latest RPD™ design technology, incorporating the complex curvatures and minimal residual stresses needed to produce the required thin walled geometry.
“We are very pleased to support ESA’s technology development efforts. The production of the expansion nozzle has provided Norsk an opportunity to apply our process to a very complex design. Norsk is confident that additive processes can be used to produce flight qualified hardware for this application in the near future,” added Carl Johnson, Norsk Chief Technology Officer.
Norsk will have a display of the Expansion Nozzle at the Farnborough International Airshow 2018, Hall 4, Booth 41430, July 16-20. For more information, visit norsktitanium.com.